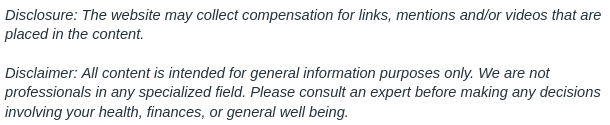
In the heart of countless industrial facilities, a workhorse quietly hums away, ensuring the smooth operation of various processes. This unsung hero is the industrial air compressor, a machine that converts mechanical power into pressurized air, typically from an electric motor or internal combustion engine. This compressed air serves as the lifeblood for various industrial applications, playing a crucial role in powering tools, machinery, and entire production lines.
The Fundamentals of Industrial Air Compressors Industrial air compressors come in various configurations, but the basic principle remains the same: taking in atmospheric air and compressing it to a higher pressure. This compressed air then becomes a versatile power source for various industrial needs.
Here’s a breakdown of the two main types of industrial air compressors:
Reciprocating Compressors: These rely on a piston moving back and forth within a cylinder to compress air. They typically have separate inlet and outlet valves that control airflow. Reciprocating compressors are known for their simplicity and durability, often preferred for applications requiring lower to moderate pressure ranges.
Rotary Compressors: As the name suggests, these utilize rotating components, such as vanes or impellers, housed within a cylindrical chamber, to compress air. Rotary compressors offer smoother operation with less vibration compared to reciprocating types. They are well-suited for continuous-duty applications and can achieve higher pressure outputs.
The Power of Multiple Stages: Achieving Higher Pressures For applications requiring even higher pressure outputs, industrial air compressors can be configured with multiple stages. In a single-stage compressor, air is compressed in one cycle. While efficient for lower pressure needs, reaching higher pressures requires additional stages. Here’s how multi-stage compression works:
Compression in Stages: Air is first compressed in the initial stage, typically the largest. Cooling Between Stages: This compressed air becomes hot. Multi-stage compressors incorporate cooling mechanisms, using air or water, to cool the air between stages. Cooling is crucial for maintaining efficient operation and safety. Further Compression: The cooled compressed air is then directed to subsequent stages for further compression, achieving even higher pressure outputs. The number of stages used in an industrial air compressor depends on the desired final pressure. For pressures exceeding 175 PSI, multi-stage compressors become essential. Some high-pressure applications can utilize as many as six or seven stages, with cooling taking place between each stage to achieve the necessary pressure.
Choosing the Right Industrial Air Compressor: Considerations for Your Needs With various types and configurations available, selecting the right industrial air compressor for your specific needs is crucial. Here are some key factors to consider:
Pressure Requirements: Identify the specific pressure needed for your intended applications. This will guide your choice between single-stage or multi-stage compressors. Air Flow Rate: The volume of compressed air your operation requires per unit of time is another critical factor. Industrial air compressors have different flow rate capacities, ensuring you have enough compressed air to power your equipment efficiently. Duty Cycle: Consider how frequently and for how long your compressor will be operating. Continuous duty applications require a different compressor type than those used intermittently. Power Source: Electric motors or internal combustion engines can power industrial air compressors. Choose the power source best suits your facility’s infrastructure and energy costs. Maintenance Needs: All machinery requires maintenance. Evaluate the ease of maintenance offered by different compressor models, considering factors like accessibility of components and service intervals. Optimizing Performance: Maintaining Your Industrial Air Compressor A well-maintained industrial air compressor ensures reliable operation, maximizes energy efficiency, and extends its lifespan. Here are some essential maintenance practices:
Regular Filter Changes: Air intake filters and oil filters (if applicable) should be replaced at recommended intervals to ensure clean air intake and proper lubrication. Oil Changes and Inspections: Following the manufacturer’s recommended oil change schedule is crucial for oil-lubricated compressors. Regularly inspect oil levels and quality. Drain System Maintenance: Drain accumulated moisture from the air receiver tank regularly to prevent corrosion and maintain efficient operation. Monitoring Performance: Regularly monitor key performance indicators such as pressure output, air flow rate, and operating temperature to identify potential issues early on. By implementing a proactive maintenance plan, you can ensure your industrial air compressor operates at peak performance, minimizing downtime and maximizing lifespan.
The Versatility of Industrial Air Compressors: Powering Your Industry Industrial air compressors are the workhorses of countless industries. Here are just a few examples of how compressed air plays a vital role in various applications:
Manufacturing: Powering pneumatic tools for assembly, drilling, grinding, and sandblasting. Construction: Operating nail guns, jackhammers, and paint sprayers.Automotive: Used in tire inflation, vehicle bodywork tools, and paint booths. Food and Beverage: Conveying materials, operating bottling equipment, and powering cleaning systems. Chemical and Petrochemical: Air purging systems, instrument air for control systems, and material transfer processes. Woodworking: Operating saws, sanders, and routers. Textile Industry: Powering looms, weaving machines, and yarn spinning equipment. Wastewater Treatment: Operating aeration systems that oxygenate water for biological treatment processes. This list is by no means exhaustive. Industrial air compressors are truly versatile and play a crucial role in numerous applications across various industries.
Conclusion: The Unsung Hero of Industry Industrial air compressors may not be the glamorous equipment, but their importance in powering countless industrial processes cannot be understated. Understanding how these machines work, selecting the right type for your needs, and implementing proper maintenance practices are crucial for ensuring they operate efficiently and reliably. The next time you witness a production line humming away in an industrial facility, remember the invisible force behind it: the power of compressed air delivered by the unsung hero, the industrial air compressor.
.